It is more crucial than ever to deliver flawless customer experiences due to the rising demand for e-commerce that is being brought on by the dependence on online purchasing. If your business conducts online product sales, you are aware that order processing is only the beginning. You can efficiently manage service, resources, and inventory with the aid of a dependable solution like Microsoft Dynamics 365 Supply Chain Management, which is a component of Dynamics 365 CRM.
You can also swiftly address product concerns, reduce delays, and quicken your time to market.
As for warehouse processes management, you have warehouse management D365.
What Is Warehouse Management D365?
Thanks to the Warehouse management module, you can manage warehouse operations in businesses engaged in manufacturing, distribution, and retail. This module includes a vast array of capabilities to support the warehousing facility at its best.
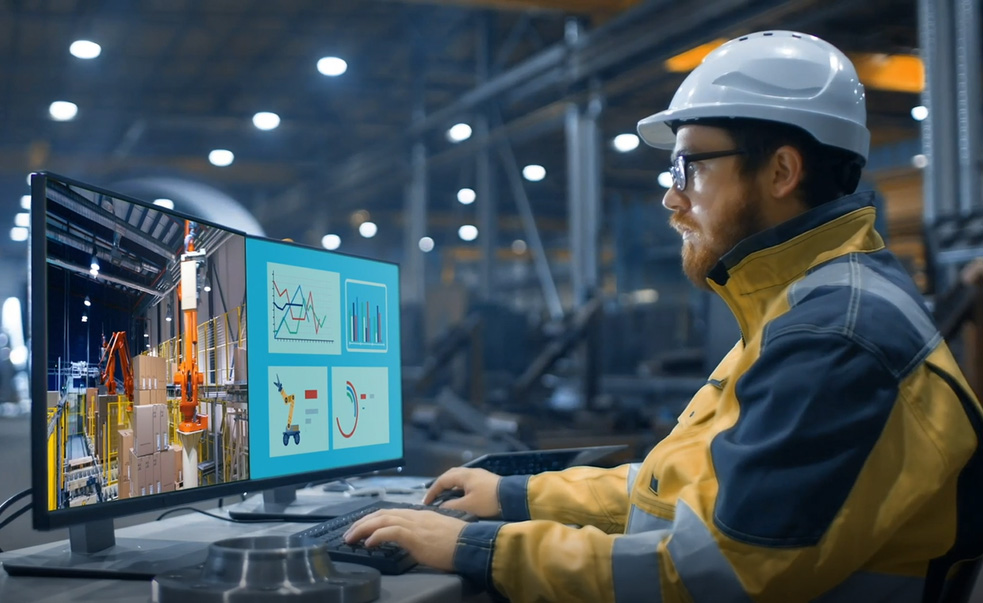
On the Work templates page, you can specify the tasks that must be completed in the warehouse. A warehouse employee typically moves the stock of goods from one location to another while carrying out their daily tasks.
In order to locate pick and put zones for inventory movement, rules known as location directives are used. A location directive, for instance, in a sales order transaction, specifies where the items will be picked up and deposited. You can create location directives, which consist of a header and related lines, on the Location directives page.
What is Supply Chain Management in Dynamics 365?
With the use of predictive analytics, Dynamics 365 Supply Chain Management allows staff members and organizations to get a unified view of inventory, warehouse, production, service, and logistics to enable better strategic decisions. Microsoft Dynamics 365 Supply Chain Management provides a deeper understanding of shipment timelines, thanks to automated order papers and improved item data.
Large-volume merchants and manufacturers can easily handle a high volume of transactions every minute and accurately identify cross-channel inventory in real-time thanks to the Inventory Visibility for Dynamics 365 Supply Chain Management ERP.
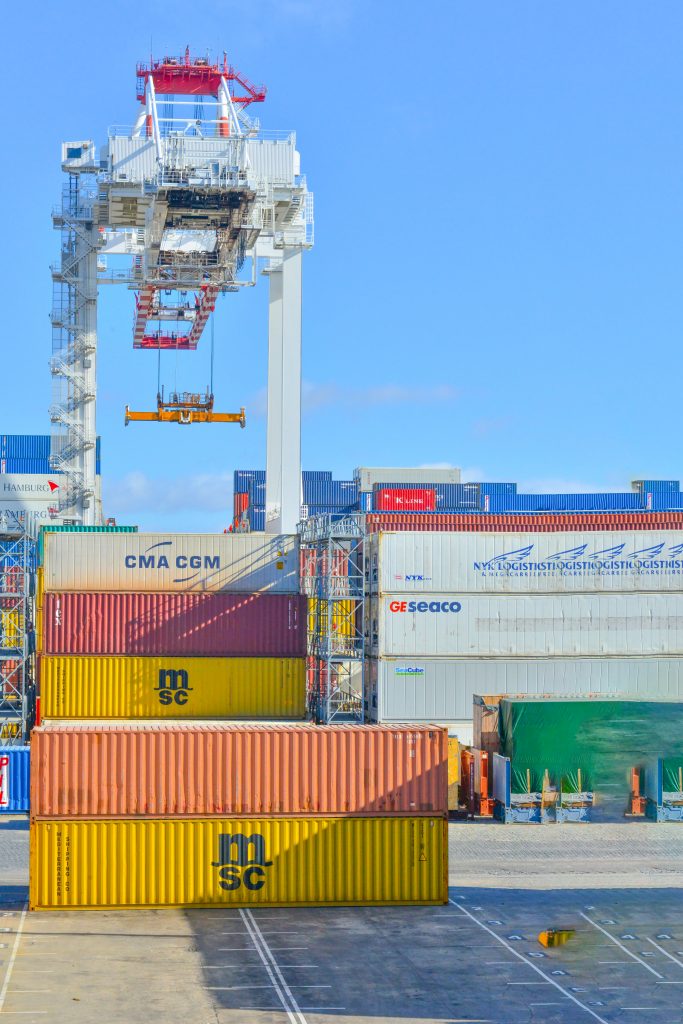
Transportation, manufacturing, quality control, procurement, transfer, sales, and returns are all fully linked with warehouse management.
Gaining real-time visibility into inbound and outbound inventory at each point of the supply chain—from the manufacturer to shipping ports to distribution centers to retailers to consumers—is essential as e-commerce grows. When a brand continually fulfills its promise to its customers, it builds affinity.
Ecommerce Warehousing Best Practices
Poor eCommerce warehousing implementation can cost brands money and potentially cause orders to be delayed. The best eCommerce warehousing techniques are followed by proper warehouse management. It boosts your revenue and offers a wonderful client experience.
An eCommerce warehouse is optimized by using the functionality provided by a warehouse management system, which is a specialized piece of software.
- Giving you immediate knowledge of your inventory and product availability.
- Managing and keeping an eye on the operations of the eCommerce supply chain, from the manufacturer to the distribution centre.
- Estimating inventory to find out when your supply may run out.
- Streamlining the eCommerce fulfillment process will increase the effectiveness of your business operations.
- Including your online store (and other tools).
- Improving inventory management to anticipate inventory more accurately, set reorder points in advance, and evaluate stock availability in real-time before a shortage occurs.
When a sale is made online, you must monitor all relevant data. The producer must be informed of this to build the product, and the 3PL must be informed to distribute it to the proper location. Data synchronization is also necessary to communicate problems like shrinkage and missed orders.
In order to automatically prepare and ship orders from the closest distribution center to the consumer after an order is placed, you can lower shipping costs by dividing your inventory among several warehouses. Offering a quicker, more affordable delivery can also enhance the client experience.
There is a wide variety of picking systems available to e-commerce enterprises. In an eCommerce warehouse, more sophisticated solutions can enable batch picking and automatically construct picking lists depending on how close together the ordered products are, reducing the number of walking paths and the amount of time it takes to pick an order.
Inventory balance is always difficult to achieve. While ordering too few products can result in out-of-stock notices, irate consumers, and lost revenue, ordering too many can hurt a company’s earnings and increase inventory-carrying expenses. A decent WMS will allow businesses to set reorder points to receive a signal anytime a product hits a certain threshold. As a result, establishing obligatory inventory minimums is a wise precaution.
Inventory is refilled according to predetermined periods while using the periodic technique. For instance, you might check the levels every three months to see if they require replacing. You don’t place new orders if the stock levels remain adequate.
If you were to use a periodic technique, you would wait to place another order until the cycle count was over, even if your inventory ran out earlier. Only at the pre-set review points are replenishment orders placed.
Get In Touch
The success of a shop depends on having the appropriate goods in the right location at the right time. Determining where inventory is fulfilled for eCommerce versus in-store orders is crucial to ensuring that consumer needs are satisfied on time and profitable as retailers and brands continue to adjust to meet the growing eCommerce demand.
So, get in touch with DHRP for quick warehouse management in dynamics 365 supply chain management implementation if you don’t want delays to haunt you or missed orders to cause you trouble.
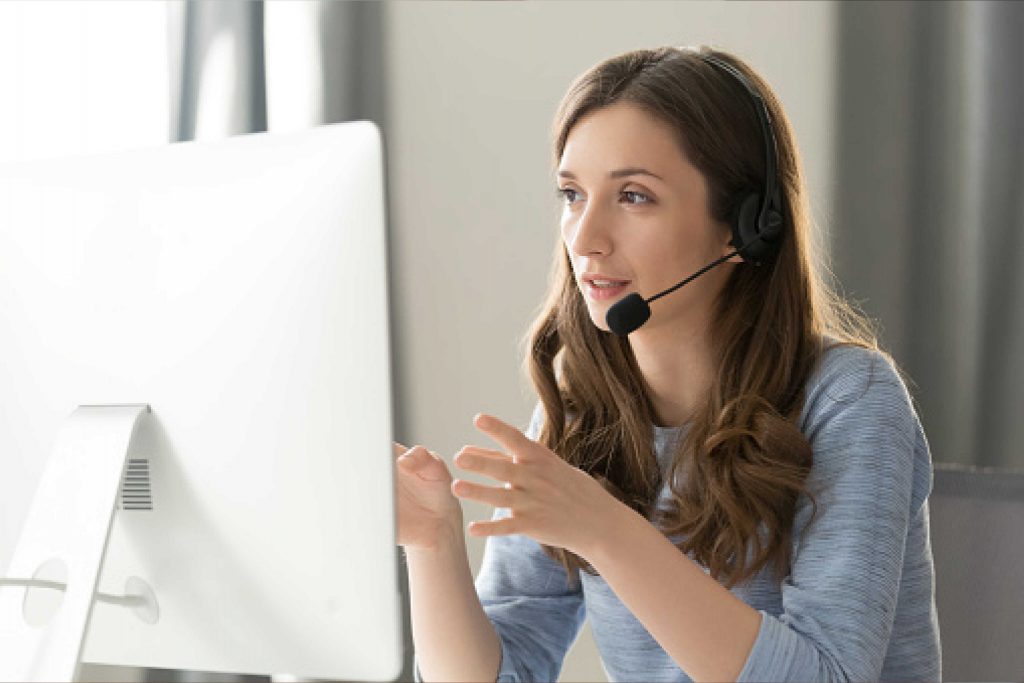